¿Solución para los residuos tóxicos de Alcoa en San Cibrao? El hidrógeno verde reconvierte lodos rojos en acero
Científicos del Instituto Max Planck descubren que a través de un proceso con hidrógeno verde se puede extraer hierro libre de dióxido de carbono del lodo rojo generado por la industria del aluminio
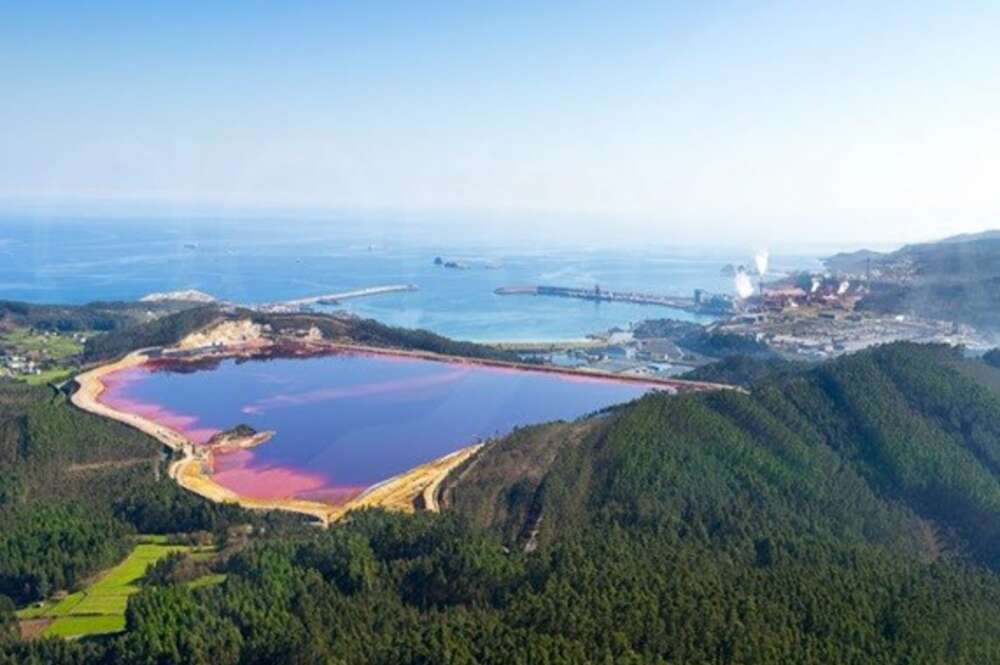
Balsa de lodos de Alcoa en San Cibrao / ADEGA
Un estudio del Instituto Max Planck de Alemania revela cómo se puede producir acero libre de dióxido de carbono a partir de los lodos rojos procedentes de la industria del aluminio, como los que pueden encontrarse en la balsa de la planta de alúmina de Alcoa en San Cibrao, situada entre las parroquias de Lago y Morás, en Xove. La multinacional presentó dos proyectos para ampliar el depósito de residuos de los 100 metros a cotas de 104 y 110 para alargar su vida útil hasta 2035 con la factoría produciendo al máximo de su capacidad y que aún están pendientes de recibir el visto bueno de la Consellería de Medio Ambiente.
La investigación de los científicos del instituto alemán revela que a través de un horno de arco eléctrico, similar a los que se emplean desde hace décadas en la industria siderúrgica, se consigue mediante plasma de hidrógeno la conversión del óxido de hierro que contiene este barro en hierro, que puede ser utilizado como materia prima en la industria del acero. Gracias a este proceso se podrían producir casi 700 millones de toneladas de acero libre de dióxido de carbono con la revalorización de los casi cuatro mil millones de lodos rojos que se acumulan actualmente a nivel mundial. Esta producción supone, aproximadamente, un tercio de la producción anual de acero de todo el mundo.
La industria aluminera genera alrededor de 180 millones de lodo rojo tóxico al año, un residuo muy alcalino que contiene trazas de metales pesados, como puede ser el cromo. Según este equipo de científicos, este barro podría llegar a revalorizarse para cubrir la demanda de acero, que llegará a crecer por encima del 60% para 2050.
Reducción por plasma
Según análisis del instituto alemán, publicado en la revista Nature, los residuos de la producción de aluminio se componen hasta en un 60% de óxido de hierro. Con un horno de arco eléctrico se funden estos lodos rojos al mismo tiempo que se reduce el óxido de hierro que contienen a hierro mediante un plasma que contiene un 10% de hidrógeno.
Este proceso, conocido en la jerga técnica como reducción por plasma, tiene una duración de diez minutos en los que el hierro líquido se separa de los óxidos líquidos para que luego pueda extraerse fácilmente. El resultado de este proceso es un hierro puro que, según los investigadores, se puede transformar directamente en acero. Los óxidos metálicos que se generan durante esta transformación ya no son corrosivos y, al enfriarse, llegan a solidificarse creando un material similar al vidrio que puede utilizarse de relleno para algunos sectores como el de la construcción.
En otros grupos de investigación se había intentado la producción de hierro a partir de lodo rojo utilizando un sistema similar pero con coque, pero esto produce hierro muy contaminado y grandes cantidades de dióxido de carbono. Sin embargo, el uso de hidrógeno verde actúa como reductor y evita estas emisiones de gases de efecto invernadero.
“Si se utilizara hidrógeno verde para producir hierro a partir de los cuatro mil millones de toneladas de lodo rojo que se han generado hasta la fecha en la producción mundial de aluminio, la industria siderúrgica podría ahorrar casi 1.500 millones de toneladas de CO2” destaca Isnaldi Souza Filho, líder del grupo de investigación en el Instituto Max Planck de Eisenforschung dedicado a la investigación relacionada con el hierro.
¿Rentabilidad económica?
Otra de las ventajas que el equipo investigador destaca de este proceso es su rentabilidad desde un punto de vista económico. Con hidrógeno y una mezcla de electricidad para el horno, procedente solo de fuentes parcialmente renovables, el proceso merece la pena, según el análisis de costes de los investigadores, si el lodo rojo contiene un 50% o más de óxido de hierro.
Si se tienen también en consideración los costes de eliminación de estos residuos tóxicos, solo un 35% de este óxido de hierro sería suficiente para que el proceso sea económico. Añadiendo a todo ello el coste actual del hidrógeno verde y la electricidad, los científicos apuntar que será necesaria una proporción entre un 30 y un 40% de óxido de hierro para que el acero resultante sea competitivo en el mercado