Carlos Moliner (Ford): «La línea entre un centro de producción y uno de innovación se está desdibujando»
El responsable de innovación y transformación de Ford Almussafes asegura: "Los gustos del consumidor cambian a una velocidad enorme, mucho más rápido que nuestra capacidad de diseñar un coche"
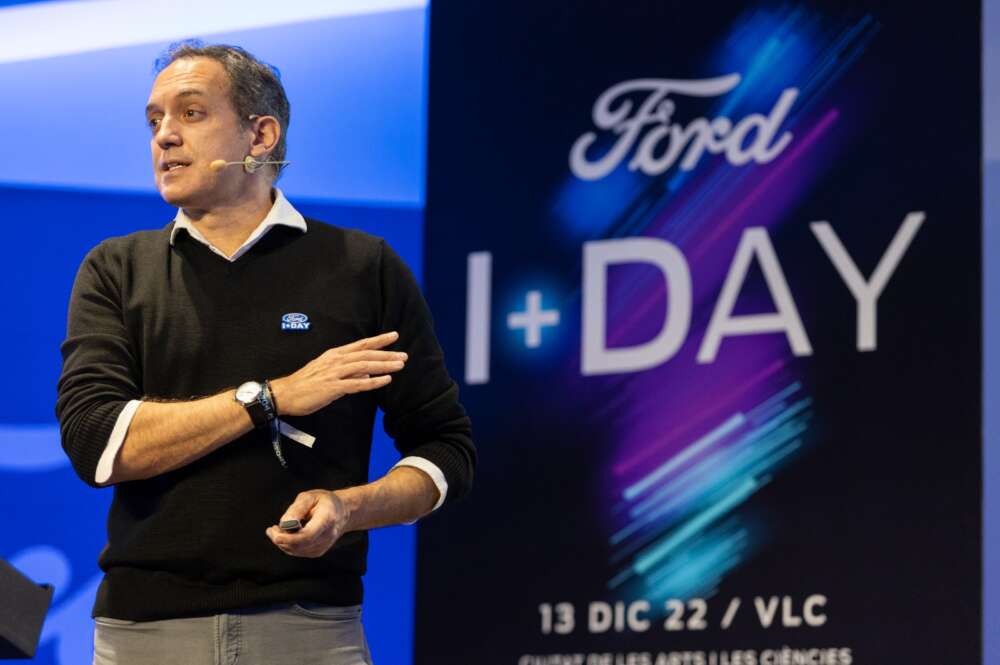
Carlos Moliner, responsable de innovación y transformación de la fábrica de Ford en Almussafes
Carlos Moliner es responsable de innovación y transformación de la fábrica de Ford en Almussafes. Atiende a Economía Digital en el contexto del I+day, un evento de nueva creación de la multinacional americana en la que por primera vez muestra la innovación que se realiza en el centro de producción valenciano. Carlos Moliner explica dónde está el foco de la innovación local, por qué se produce y cómo ha cambiado la posición de la fábrica tras los avances que ha implementado.
Pregunta: ¿Cuáles son los objetivos de la innovación dentro de la factoría de Almussafes?
Respuesta: A nuestro primer bloque innovacion le llamamos fabricación flexible. Partimos de la base de que tenemos una cadena de suministro inestable. Iba a ser para el Covid y recuperación del Covid pero está durando y no sabemos cuándo vamos a volver a un régimen normal. Los gustos del consumidor cambian a una velocidad enorme, mucho más rápido que nuestra capacidad de diseñar un coche. Lanzarlo con todo el proceso tradicional es demasiado largo para lo que necesita el cliente. El hecho de tener todo conectado entre sí dentro de la planta y estar interconectado con los proveedores supone que hay una cantidad de información que nos permite que la cadena de producción reaccione más rápido que lo que hacía hasta ahora. El objetivo es cómo conseguimos desacoplar la cadena de producción para que no sea una línea continua. El concepto de una línea continua de producción de Henry Ford ya no va a continuar. Cómo lo desacoplamos en trozos más pequeños que sigan siendo eficientes, reduzcan costes y permitan reaccionar con velocidad es nuestro reto.
¿Qué pilares hay en su plan de innovación?
La robotización avanzada es todo lo que tiene que ver con la automatización. Esto es hacer operaciones de forma estándar y más rápida y cómo somos capaces de hacer cambios los más rápido posible. Son los cobots, robots colaborativos que trabajan al lado del operario. No es el concepto del robot grande que había antes sino equipos más flexibles.
El siguiente pilar es la visión artificial.
Buscamos mejorar la calidad y verificar el 100% de las piezas con características críticas que validan bueno o no bueno. Este es el concepto clásico, pero si a un robot le pones una cámara, el robot gana inteligencia y ésta es una de las sinergias que estamos desarrollando. El robot es capaz de identificar y seleccionar en un entorno caótico y eso da una flexibilidad enorme
El tercer pilar son los AGV. ¿Qué significa?
Es la logística autónoma. Son vehículos autónomos antes guiados y ahora con más inteligencia para repartir las piezas por la línea. Estamos arrancando un proyecto que es tener un robot encima de un AGV para que sea móvil.
«La impresión 3D genera ahorros desde el momento cero. Estamos haciendo recambios de la pieza de la línea que antes comprábamos fuera»
El último es la impresión 3D .
Es el que más ahorros reales está dando. Mientras el resto son tecnologías habilitadoras que nos permiten tener potencial, la impresión 3D genera ahorros desde el momento cero. Estamos haciendo recambios de la pieza de la línea que antes comprábamos fuera. Primero eran carísimas y ahora tardan mucho en llegar. Las estamos imprimiendo en 3D. Tenemos reducción de costes, de peso y disponibilidad inmediata.
Recientemente, Economía Digital informó del concurso de acreedores de Matrival, histórica empresa de moldes para Ford. ¿Hay futuro para el sector de los moldes o va a virar la automoción hacia el 3D?
Son complementarios. Estamos haciendo piezas 3D no para coches. Las utilizamos para la línea de producción como recambios. La impresión 3D puede ser interesante hasta cierto volumen. Para una producción en masa tienes que irte a molde, no va a ser rentable hacerlo en 3D. Quizá en 5 años ha cambiado la tecnología, pero ahora mismo es complementario y no sustituye una a otra.
¿Prevé que la impresión 3D pueda reducir las piezas que se piden a proveedores?
No somos capaces de fabricar en impresión 3D las piezas que se montan en los coches. Harían falta tantísimas máquinas que al final es económico tener un molde.
¿Para qué tipo de necesidades está el 3D?
Nosotros no lo utilizamos. Para vehículos de producción muy cortas tendría sentido pero cuando hay más de 2.000 o 3.000 hay que hacer números. A nosotros nos sirve para producción. Nos sirve para las garras de los robots. Eso es un ‘business case’ inmediato”.
Los coches antes duraban un cuarto de siglo. 4 años de diseño, 8 de producción y otros 12 funcionando y ahora detectáis que los gustos cambian más rápido que lo que evoluciona el producto en fábrica. ¿Cómo afrontáis este cambio?
La combinación de robots colaborativos, AGV y visión por la parte de inteligencia que aporta nos permite cambiar los elementos de la línea de producción de una manera mucho más ágil que antes. Esto nos da flexibilidad en las operaciones en sí. Lo que antes era una inversión mucho más grande para desarrollar un modelo ahora se acorta mucho el proceso de poner al día una planta.
¿Va a cambiar el tiempo de vida de una plataforma de la automoción?
Hay dos visiones y eso es lo que se está debatiendo ahora. ¿Vamos a tener un hardware que se va a actualizar con software de manera que el hardaware va a durar mucho o vamos a seguir pensando que el software cambia cada tres o cuatro años? No sé contestarte porque se esta debatiendo.
«La ventaja de Tesla es que parte de cero y nosotros tenemos una herencia que tenemos que ir modificando»
Cuando se habla de competir con Tesla, ¿os referís más a la forma de producir que al propio producto en sí?
En lo que es el sistema productivo, la lucha es diferente. La ventaja de Tesla es que parte de cero y nosotros tenemos una herencia que tenemos que ir modificando. La competencia con Tesla es en el producto, por que cada uno lo hace de una manera diferente. Es muy diferente partir de cero que tener una planta y modificarla. El reto es conjugar procesos que ya tengo y en los que soy experto con proyectos nuevos en los que tengo de desarrollar talento. Y esa es la tendencia de innovación que tenemos.
El llamado mayor cambio en la historia del automóvil desde la creación de la cadena de producción de Henry Ford, ¿a que os referís?
A un mecanismo de producción mucho más flexible. Me cuesta contestar a este concepto porque, por un lado es estratégico (confidencial) y, por otro, porque estamos en fase de pruebas.
Antes el centro de innovación creaba el producto y el de producción lo fabricaba y ahora el centro de producción está cambiando los procesos con funciones que antes no tenía.
Con la llegada del vehículo eléctrico y conectado hay una parte que tiene capacidad de conectarse con todo: el cliente, con la ciudad… Dentro de esa capacidad está también la capacidad de conectarse con la propia línea de producción. Con ello, la cantidad de conexiones y de automatización flexible explota. No puedo ir más allá, pero los tiros van por ahí. Es cierto que la línea entre el centro de innovación y el de producción se está desdibujando.
«Los cobots (robots colaborativos) han nacido aquí y se están replicando tanto en Europa como en Estados Unidos»
Tal y como habéis mostrado en el I+day, la creación desde Almussafes de estándares de producción a nivel mundial supone que desde aquí estáis cambiando la forma de fabricar de Ford en el mundo.
Sí. Los casos son los cobots que han nacido aquí y se están replicando tanto en Europa como en Estados Unidos. Las aplicaciones son robots colaborativos para una determinada función. Eso se ha desarrollado aquí y lo están copiando en Esados Unidos y en Europa. Somos el estandar que está siguiendo Ford en el mundo tanto en robotos colaborativos como en vehículos de reparto autónomo.
¿Qué es lo que más llama la atención a los directivos americanos que vienen a Valencia a ver las innovaciones?
La discusión siempre acaba en lo siguiente: la cultura. Vienen y hacen preguntas. La cultura es el resultado de lo que es este sector desde que nació encima de un campo de naranjos. En los años 70, una serie de emprendendores locales y unas grandes empresas se pusieron a trabjar y hay un espíritu ahí y un germen de colaboración y de emprendedurismo que sigue existiendo hoy y que es lo que hemos heredado como sector.
¿El factor colaborativo es el diferencial por la implicación de la plantilla en los cambios?
El factor colaborativo y la cultura de excelencia que, con el paso del tiempo, se ha convertido en cultura de innovacion. Estos son los elementos que son muy difíciles de copiar fuera. Estos factores están en los empleados y lo mencionaba Dionisio Campos durante la jornada de I+day. Valencia es de las pocas plantas en las que el empleado está implicado en el mantenimiento porque sienten que la operación es suya y que el resultado de lo que pasa en el dia a día es de todos. Esto es muy complicado de replicar. Mi opinión personal es que viene de cómo se ha generado este sector desde los años 70.
Cuando hablais de la innovación en la planta aseguráis que se debe a un ecosistema valenciano de pymes y startup así de como universidades. ¿Qué características tienen para que sean capaces de hacer estándares que Ford aplica a nivel global?
Llevo 15 años en temas de I+D y la evolución que he visto en las pymes es que ahora se hacen proyectos de innovación sin complejos y sin plantearse si son punteros o no. Se hace sin mirar a Alemania, ni China ni Japón ni Estados Unidos.
«Hubo un proceso de profesionalización en el sector gracias a la UPV»
¿Qué aportan las universidades?
Volviendo a los años 80, hubo un proceso de profesionalización en el sector gracias a la UPV enorme en el que llegó una cantidad de gente a las empresas con conocimiento de métodos enorme, procesos, conceptos de mejora continua que permitió una profesionalización brutal. Lo que estoy viendo en los últimos dos o tres años es que a esto se añade que están siendo capaces de generar perfiles en ciencia de datos y digitalización y visión artificial que eran impensables hace seis o siete años.
Sin confirmación de nuevos modelos, no estamos en una rampa de lanzamiento sin en modificaciones cada 8 días del calendario de ERTE. ¿En qué medida afecta la situación actual a la innovacion?
Nos afecta en un esfuerzo enorme para interpretar y acetar el tiro con losoryecots que tenemos que realizar. Tenemos siete pilares en los que trabajamos y eso es independiente de lo que pase en la línea. Lo que nos afecta es que tenemos que imaginar dónde vamos a estar dentro de tres años. Es más fácil si sabes lo que va a venir y tienes la visión clara de qué va a venir y sino, pues a buscar y desarollando proyectos en la niebla.
Vuestro trabajo es una vez conocido el hardware y cómo va a ser la línea de producción. ¿Está claro ya el hardware que va a tener Almussafes?
Se esta definiendo. Hay elementos ya claro que nos permiten tener líneas de producicón mucho más claras y otras en las que hay interroganes en las que barajamos distintas alternativas. Esto en cosas como robotización o 3D me da igual. Puedo seguir avanzando. En aspectos como conectividad en la que se decida la tecnología a utilizar va a afectar a mis desarrollos de innovación.
¿Puede alguna de las innovaciones que realizais modifique futuras plataformas?
No creo que llegemos a tanto.
«Estamos desarrollando el talento en interno. No hemos salido al mercado a contratar a gente»
¿El presupuesto de innovación para el año que viene aumenta o disminuye?
(Risas) Se lo voy a preguntar a Dioni(sio Campos, director de la fábrica). Espero que haya aumentado. Me lo tiene que decir.
¿Van a haber contrataciones?
Estamos desarrollando el talento en interno. No hemos salido al mercado a contratar a gente. Queremos que el conocimiento se quede dentro de casa.
Con la llegada de otro jugador a Valencia, ¿temeis perder talento con la llegada de Volkswagen?
Que haya otro jugador aquí y con el espírtu colaborativo, sólo puede haber crecimiento para todos. Más allá de que pueda ser incómodo, va a ser bueno.